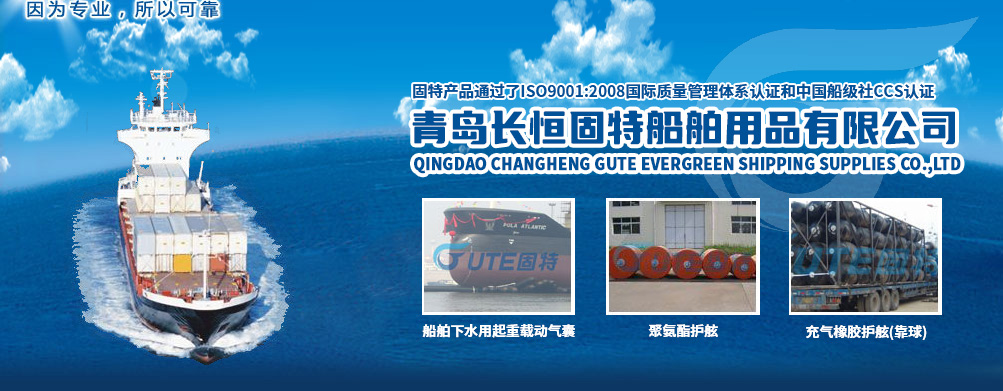



主要產(chǎn)品:船舶下水用起重載動氣囊,充氣橡膠護(hù)舷(靠球),聚氨酯護(hù)舷,游艇專業(yè)碰墊。產(chǎn)品選用優(yōu)質(zhì)的材料和特殊的防爆工藝,外觀光順、耐磨、耐老化、氣密性好、強(qiáng)度高,使用壽命長,質(zhì)量過硬,并通過了ISO9001 :2000國際質(zhì)量管理體系認(rèn)證,和中國船級社(CCS)質(zhì)量認(rèn)證。




-
新聞中心
當(dāng)前位置:首頁 - 新聞中心
-
橡膠硫化工藝方法
發(fā)布時間:2018.05.26 新聞來源:青島固特船舶用品有限公司 瀏覽次數(shù):橡膠硫化工藝方法
一、傳統(tǒng)橡膠硫化工藝
1、影響硫化工藝過程的主要因素:
硫磺用量。其用量越大,硫化速度越快,可以達(dá)到的硫化程度也越高。硫磺在橡膠中的溶解度是有限的,過量的硫磺會由膠料表面析出,俗稱“噴硫”。為了減少噴硫現(xiàn)象,要求在盡可能低的溫度下,或者至少在硫磺的熔點(diǎn)以下加硫。根據(jù)橡膠制品的使用要求,硫磺在軟質(zhì)橡膠中的用量一般不超過3%,在半硬質(zhì)膠中用量一般為20%左右,在硬質(zhì)膠中的用量可高達(dá)40%以上。
硫化溫度。若溫度高10℃,硫化時間約縮短一半。由于橡膠是不良導(dǎo)熱體,制品的硫化進(jìn)程由于其各部位溫度的差異而不同。為了保證比較均勻的硫化程度,厚橡膠制品一般采用逐步升溫、低溫長時間硫化。
2、硫化時間:這是硫化工藝的重要環(huán)節(jié),時間過短,硫化程度不足(亦稱欠硫)。時間過長,硫化程度過高(俗稱過硫)。只有適宜的硫化程度(俗稱正硫化),才能保證最佳的綜合性能
二、橡膠硫化工藝方法
按硫化條件可分為冷硫化、室溫硫化和熱硫化三類。
1、冷硫化可用于薄膜制品的硫化,制品在含有2%~5%氯化硫的二硫化碳溶液中浸漬,然后洗凈干燥即可。
2、室溫硫化時,硫化過程在室溫順常壓下進(jìn)行,如使用室溫硫化膠漿(混煉膠溶液)進(jìn)行自行車內(nèi)胎接頭、修補(bǔ)等。
3、熱硫化是橡膠制品硫化的主要方法。根據(jù)硫化介質(zhì)及硫化方式的不同,熱硫化又可分為直接硫化、間接硫化和混氣硫化三種方法。
①直接硫化,將制品直接置進(jìn)熱水或蒸汽介質(zhì)中硫化。
②間接硫化,制品置于熱空氣中硫化,此法一般用于某些外觀要求嚴(yán)格的制品,如膠鞋等。
③混氣硫化,先采用空氣硫化,而后再改用直接蒸汽硫化。此法既可以克服蒸汽硫化影響制品外觀的缺點(diǎn),也可以克服由于熱空氣傳熱慢,而硫化時間長和易老化的缺點(diǎn)。
三、橡膠硫化工藝:
橡膠在未硫化之前,分子之間沒有產(chǎn)生交聯(lián),因此缺乏良好的物理機(jī)械性能,實(shí)用價值不大。當(dāng)橡膠加進(jìn)硫化劑以后,經(jīng)熱處理或其他方式能使橡膠分子之間產(chǎn)生交聯(lián),形成三維網(wǎng)狀結(jié)構(gòu),從而使其性能大大改善,尤其是橡膠的定伸應(yīng)力、彈性、硬度、拉伸強(qiáng)度等一系列物理機(jī)械性能都會大大進(jìn)步。橡膠大分子在加熱下與交聯(lián)劑硫磺發(fā)生化學(xué)反應(yīng),交聯(lián)成為立體網(wǎng)狀結(jié)構(gòu)的過程。經(jīng)過硫化后的橡膠稱硫化膠。硫化是橡膠加工中的最后一個工序,可以得到定型的具有實(shí)用價值的橡膠制品。
四、注壓成型硫化工藝:
普通模壓與注壓最明顯的區(qū)別在于前者膠料是以冷的狀態(tài)充進(jìn)模腔的,而后者則是將膠料加熱混合,并在接近硫化溫度下注進(jìn)模腔。因而,在注壓過程中,加熱模板所提供的熱量僅僅只用于維持硫化,它能很快將膠料加熱到190℃-220℃。在模壓過程中,由加熱模板所提供的熱量首先要用于預(yù)熱膠料,由于橡膠的導(dǎo)熱性能差,假如制品很厚,熱量要傳導(dǎo)到制品中心需要較長的時間。采用高溫硫化也可在一定程度上縮短操縱時間,但往往導(dǎo)致靠近熱板的制品邊沿出現(xiàn)焦燒。采用注壓法硫化,可以縮短成型周期,實(shí)現(xiàn)自動化操縱,這對大批量生產(chǎn)最為有利。注壓還具有以下優(yōu)點(diǎn):可以省往半成品預(yù)備、起模和制品修邊等工序;可以生產(chǎn)出尺寸穩(wěn)定、物理機(jī)械性能優(yōu)異的高質(zhì)量產(chǎn)品;減少硫化時間,進(jìn)步生產(chǎn)效率,減少膠料用量,降低本錢,減少廢品,進(jìn)步企業(yè)經(jīng)濟(jì)效益。
五、注壓成型硫化工藝留意事項(xiàng):
采用公道的螺桿轉(zhuǎn)速、背壓,控制適當(dāng)?shù)淖⑸錂C(jī)溫度。一般地,應(yīng)保持出料口膠溫順控制循環(huán)溫度之差不大于30度為宜。注射機(jī)螺桿的用途是在選定的和均勻的溫度下為每一循環(huán)制備足夠量的膠料;它明顯地影響著注射機(jī)的產(chǎn)量。背壓是通過放慢注射缸中出油口的流量而產(chǎn)生的,并對注射機(jī)所射出膠料,對注射油缸的推擠作用進(jìn)行限制。實(shí)踐中,背壓只會稍微增加對膠料的剪切,而不會引起硫化制品物理性能的降低。
噴嘴的設(shè)計(jì):
噴嘴連接注射機(jī)頭和模具,同時對熱平衡有一定作用。經(jīng)過噴嘴的壓力損失會經(jīng)過注射而轉(zhuǎn)換成為熱量。膠料盡不答應(yīng)在這個部位硫化。因此,選擇合適的噴嘴直徑非常重要,它影響著噴嘴部位的摩擦生熱、膠料注射時所需要的壓力和充模時間。
合適的模具溫度,最佳的硫化條件。在選擇好膠料的最佳配合之后,重要的就是注射成型條件與硫化條件的相互配合。注壓成型與模壓成型相比,由于模具表面、內(nèi)部溫度分布不同,要實(shí)現(xiàn)良好的硫化就必須對溫度進(jìn)行高精度控制,使模具表面、內(nèi)部同時達(dá)到最佳硫化條件。高溫會增大橡膠的收縮率,但二者關(guān)系是線性的,在生產(chǎn)前應(yīng)有充分的估計(jì)。此外,就成型壓力而言,高壓成型是極為有利的,由于壓力與收縮成反比關(guān)系。
安全公道的膠料配方設(shè)計(jì)。對于進(jìn)行注壓硫化成型的膠料,要求其具有以下特性:
膠料的門尼焦燒時間應(yīng)當(dāng)盡可能的長,以獲得最大的安全性。通常,門尼焦燒時間應(yīng)比膠料在機(jī)筒中的停留時間長2倍。
硫化速度快,通過對不同膠料硫化體系的公道選擇,添加合適的促進(jìn)劑,使膠料在注壓硫化時有令人滿足的效率;顒有粤己,良好的活動性能減少膠料的停留時間,減少注壓時間,并進(jìn)步防焦燒能力。
六、氮?dú)饬蚧に?nbsp;
采用充氮?dú)饬蚧闹饕獌?yōu)點(diǎn)是節(jié)能和延長膠囊壽命,可節(jié)省蒸汽80%,膠囊使用壽命可延長1倍。輪胎在硫化過程中要消耗大量熱能和電能,因此開發(fā)和推廣節(jié)能硫化工藝意義重大。由于氮?dú)夥肿恿啃 崛莺苄,氮(dú)獬溥M(jìn)輪胎膠囊內(nèi)腔時,不會吸熱而引起溫度降低,也不易造成膠囊氧化裂解破壞。
七、氮?dú)饬蚧墓に囂攸c(diǎn)
先通高溫高壓蒸汽,若干分鐘后切換通進(jìn)氮?dú),利用充氮硫化的“保壓變溫”工藝硫化至結(jié)束。由于最初通進(jìn)幾分鐘蒸汽的熱量足夠保持硫化一條輪胎,理論上只要在完成硫化之前溫度不降到150℃以下即可。但是,采用氮?dú)饬蚧瘯r,首先通進(jìn)的是高溫高壓蒸汽,會造成上下胎側(cè)的溫差,要消除上下胎側(cè)的硫化溫差,必須公道布置硫化介質(zhì)噴射的位置,改進(jìn)密封和熱工管路系統(tǒng)。硫化用氮?dú)獾募兌纫筮_(dá)99.99%,最好達(dá)到99.999%,并建議企業(yè)自配制氮系統(tǒng),以降低使用本錢。氮?dú)饧兌炔粔,會影響膠囊的使用壽命。 將氮?dú)饬蚧摹氨鹤儨亍绷蚧響?yīng)用于傳統(tǒng)循環(huán)過熱水硫化工藝的改造,人們又開發(fā)出了用高溫高壓蒸汽加過熱水的硫化工藝取代常規(guī)的循環(huán)過熱水硫化工藝。硫化時,先通進(jìn)高溫高壓蒸汽,若干分鐘后切換通進(jìn)循環(huán)過熱水,再過若干分鐘后封閉回水閥停止循環(huán),直到利用潛熱硫化至結(jié)束。采用這種新的加熱硫化方法,據(jù)理論計(jì)算,其能耗僅是傳統(tǒng)硫化工藝方法的1/2。
八、變溫硫化工藝
變溫硫化工藝過程的關(guān)鍵因素
根據(jù)成品物理性能試驗(yàn)和生產(chǎn)經(jīng)驗(yàn),縮短硫化時間。這在一定程度上減輕了過硫化程度。
采用高溫硫化。近年來小型輪胎硫化工藝逐漸向高溫硫化方向發(fā)展,且考慮后硫化效應(yīng),硫化時間短,對減輕過硫和進(jìn)步硫化程度的均勻性有一定作用。
進(jìn)行硫化測溫,找到制品中的最慢硫化點(diǎn),以該點(diǎn)為依據(jù)來確定硫化時間,效果較前兩種好。利用該法可不同程度地進(jìn)步硫化效率,改善硫化程度的均勻性。但由于實(shí)際生產(chǎn)中只考察外溫,輪胎各部位的實(shí)際溫度并不確知,加上并不是每次溫度固定不變,因此根據(jù)測溫計(jì)算出的結(jié)果與實(shí)際硫化的結(jié)果有較大誤差。 橡膠厚制品硫化過程溫度場模擬仿真與猜測表明,溫度不均勻是造成輪胎外胎硫化程度不均勻的主要因素。橡膠產(chǎn)業(yè)普遍以為外溫恒定是保證質(zhì)量的重要條件,從設(shè)備上要千方百計(jì)地實(shí)現(xiàn)恒溫。這對非厚橡膠制品來說是正確的,而對輪胎外胎等厚橡膠制品則不然。輪胎在模型中加熱硫化,熱經(jīng)過模型傳到外胎各部位。橡膠是熱的不良導(dǎo)體,溫升慢,加熱早期外胎各部位存在明顯的溫度梯度,經(jīng)過較長時間才能達(dá)到平衡。
橡膠護(hù)舷|橡膠氣囊|專業(yè)生產(chǎn)廠家青島固特船舶用品有限公司

